Collaboration is not about agreement. It is about creation. As Michael Schrage puts it in his book, Shared Minds:
"...collaboration is the process of shared creation: two or more individuals with complementary skills interacting to create a shared understanding that none had previously possessed or could have come to on their own. Collaboration creates a shared meaning about a process, a product, or an event. In this sense, there is nothing routine about it. Something is there that wasn't there before."
Design of complicated systems like automobiles require many design teams with different expertise. These teams in themselves is not enough. How effective the team is in collaborating is often a direct measure of how successful the design is. The most important goal of this AUTO21 project is to study collaboration in automotive design engineering and recommend how collaboration can be improved.
Several collaboration tools and methods used and studied in this project:
- TCC (Team Center Community): is a huge collection of interacting software elements, basically web-driven, but with a large underlying database system. Ideally suited to track documentation, including CAD files, but not necessarily as usable as it should be to be "lightweight".
- TWIKI: This is similar to TCC and through it, information about different systems are posted and every designer from any group can use that information.
- CMaps: Concept maps are graphical tools for organizing and representing knowledge. They include concepts, usually enclosed in circles or boxes of some type, and relationships between concepts indicated by a connecting line linking two concepts. At the beginning of the project TCC was used and after about 1 year of using, it was replaced by TCC.
- MSN
- Phone
Static and Dynamic Analysis
Dr. Kim and his students have been involved in a multi-site, multidisciplinary engineering project funded by AUTO21. This project involves collaboration with various Canadian universities as well as industry sponsors such as General Motors. The goal of the project is to investigate collaborative tools and methodologies as they apply to engineers. To study collaboration, participants have undertaken the task of designing a zero emission vehicle.
The structural research group's task in this project has been chassis design with focus on multidisciplinary optimization. The chassis design and optimization have been performed considering weight, crashworthiness, stiffness, and natural frequency.
Preliminary exterior concept sketches were utilized to develop an initial chassis design.
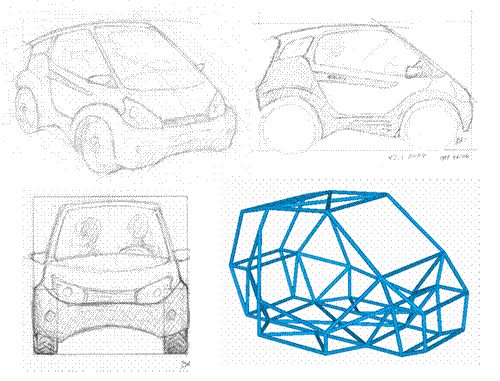
Sketches by David Killing
Utilizing ANSYS FEA software, static analyses of bending and torsional stiffness, as well as natural frequency, have been conducted. In the bending loading case, all four suspension points were fixed and a load was applied downward to the centre of the chassis. In the torsional loading case, rear suspension points were fixed while a torque was applied to the front. The inverse of this loading was also examined to eliminate front/rear bias of results. Modal analysis was also performed to determine the natural frequency of the chassis.
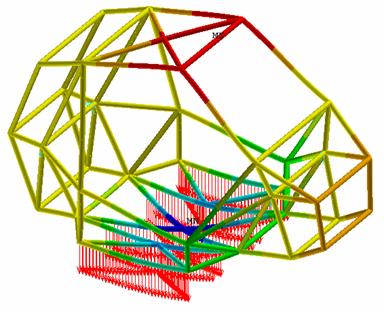
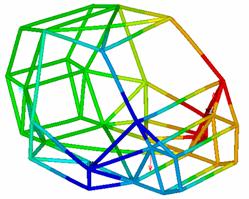
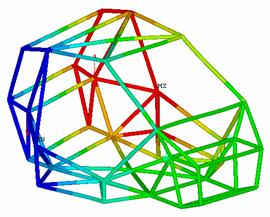
The static and dynamic simulations were then combined into an optimization routine using the MATLAB optimization toolbox. The goal of this optimization was to minimize chassis weight by iterating tubing size (increasing vehicle performance and efficiency), while maintaining benchmark structural stiffness and crashworthiness values.
Optimization Problem Definition
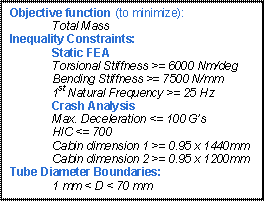
Optimization Results
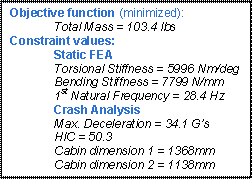
Initial Design Optimized Design
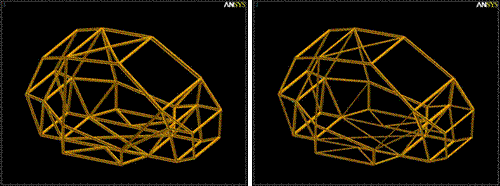
To examine dynamic behaviour of the chassis, LS-DYNA dynamic FEA software was utilized along with ANSYS and MATLAB to conduct crashworthiness simulations. To address the limitation of the chassis alone being modeled in the crash simulation, non-structural point masses were added in key areas to obtain a more realistic total vehicle mass and mass distribution. The weight of the chassis was reduced from 139 kg to 103.4 kg. The optimization routine maintained benchmark structural and crashworthiness values. Crashworthiness was visibly improved, with increased deformation and energy absorption at the front of the chassis without significant cockpit deformation.
Before Optimization
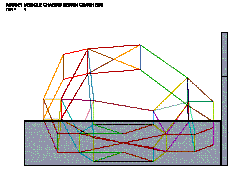
After Optimization
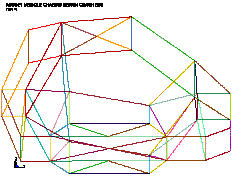
Further work in chassis development will include revisions to the design for improved manufacturing and suspension mounting, as well as to allow for integration with exterior vehicle design. Also, the optimization will be revised to take into account additional loading scenarios, and the crashworthiness simulation will be improved by using more realistic mass distributions.
Chassis Design Guide
One of the main deliverables of this project is a complete and comprehensive chassis design guide. This project is unique in that this design is developed from the conceptual stages all the way to building and manufacturing. This facilitates the documentation of the design process and procedures needed for a complete chassis design. It covers conceptual methodologies, preliminary and detailed analysis techniques and manufacturing strategies.
An added dimension to this design is the collaboration aspect. The chassis is an integral part of any automobile and thus the decisions made in its design affect just about every other subsystem. One cannot simply make changes as they wish or strictly based on performance. On the contrary, most decisions must be made collectively which often requires a compromise of at least one design variable or another. This design guide indicates key areas of interaction and collaboration and helps identify the design web and hierarchy.